Japanese lacquer, or urushi, is the clarified sap of the Asian lacquer tree, which has been used in Japan for thousands of years to coat items such as tableware, furniture and buildings. When dried, the lacquer is both heat and water resistant and therefore provides protection and strength to the underlying materials, very often wood, but also bamboo, paper and leather. Lacquerware itself can be referred to as both urushi and shikki 漆器 (literally "urushi vessel"), and with the development of acrylic resin in the last century, objects coated with synthetic lacquers such as food-grade polyurethane are also considered urushi/shikki. Pure urushi is transparent, while the black and red lacquer colors most commonly associated with shikki are achieved by adding mineral pigments. On top of this, traditional decorative details such as golden maki-e "scatter images" or shell inlays called "raden" can be added
Teacup Sakura
Fuki Tamago
Gato Mikio
Type | Teacup |
Studio/Artist | Gato Mikio 我戸幹男 |
Origin | Yamanaka, Ishikawa, Japan |
Capacity | 190ml |
Dimensions in cm | Ø8,3 x 8,1 |
Material | Japanese bird cherry |
Glaze | Food safe polyurethane varnish |
Manufacturing | Made in Rokuro-biki technique, where the wood is processed by hand on a wheel. Requires a lot of experience and skill. |
Stamp | Studio Stamp |
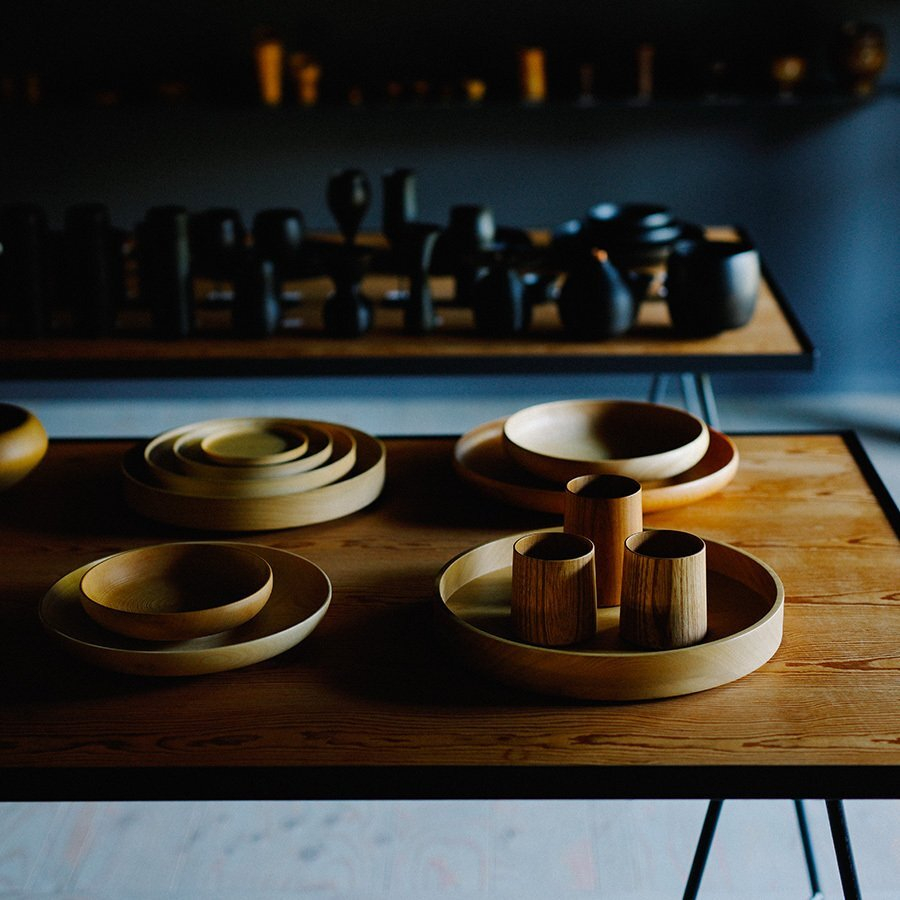
GATO MIKIO 我戸幹男
Winner of numerous national and international design awards, the traditional manufacturer GATO MIKIO was founded in Yamanaka Onsen (山中温泉) in 1908 by master wood turner Komakichi Gato. The small hot spring resort (onsen, 温泉) is famous from the travelogue "The Narrow Path to the Deep North" (Oku no Hosomichi, 奥の細道), a major work of Japanese literature by the national poet Basho, who praises the hot springs (Jap. onsen) for their rejuvenating waters. The humid climate in the region is ideal for working with urushi and Japanese lacquer ware. Today, GATO MIKIO is run by the fourth generation of Masayuki Gato, who is dedicated to preserving the Yamanaka shikki traditions and carrying them forward in harmony with the demands of the modern world. The vertical tatekidori cutting method characteristic of Yamanaka shikki is used to cut the wood, which makes the wood more stable and brings out the striking patterns of the wood grain in particular. To further enhance the natural beauty of the wood and decorative woodwork, GATO MIKIO prefer to use the fuki-urushi (拭漆): "wiping varnish" technique (also known as suri-urushi (摺り漆) "rubbing varnish") for their Yamanaka Shikki, in which a clear varnish is rubbed into the wood to highlight the natural wood grain. The raw varnish is applied with a brush, then evenly distributed and wiped off, and finally carefully polished with sandpaper. This process is repeated five or six times and can take several months, with each coat adding strength and shine to the vessel.This particular attention to material and detail clearly demonstrates the two central principles of the traditional manufactory. On the one hand, the preservation of local heritage, and on the other, a "return to origin" (genten kaiki 原点回帰). Keeping in mind Yamanaka's heritage as a manufacturing site for souvenirs for onsen visitors, GATO MIKIO creates objects that are not only aesthetically pleasing, but also practical and adapted to modern times. To achieve this, the master artisans collaborate with Japanese designers to create new shikki interpretations of traditional-minimalist beauty and modern appeal. Nonetheless, the manufactory is very concerned with preserving Yamanaka shikki traditions and maintaining the local craftsmanship and artisan community.
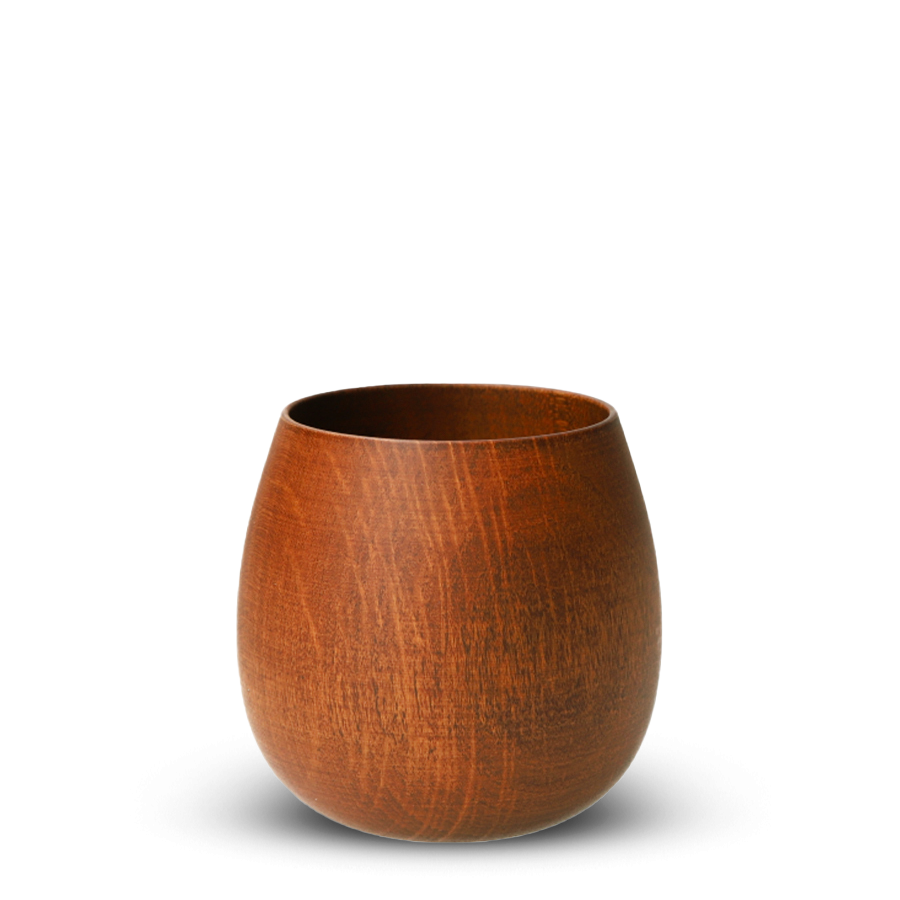
Yunomi 湯のみ
Literally a "utensil for drinking hot water," the yunomi is a tall, cylindrical Japanese tea cup that is typically made of ceramic and has no handle. It is ideal for everyday drinking and for all types of tea - except matcha, which is best served in the more formal chawan (or matchawan) tea cup. Ideally, the yunomi is held with both hands: one hand around the cup to hold it and the other underneath to support it. Since even hotter brewed Japanese teas such as houjicha, genmaicha, and bancha are served at a temperature below 80°C / 175°F, the yunomi itself does not get too hot, yet provides additional warmth for the hands during the colder months, making it particularly suitable for enjoying these winter teas
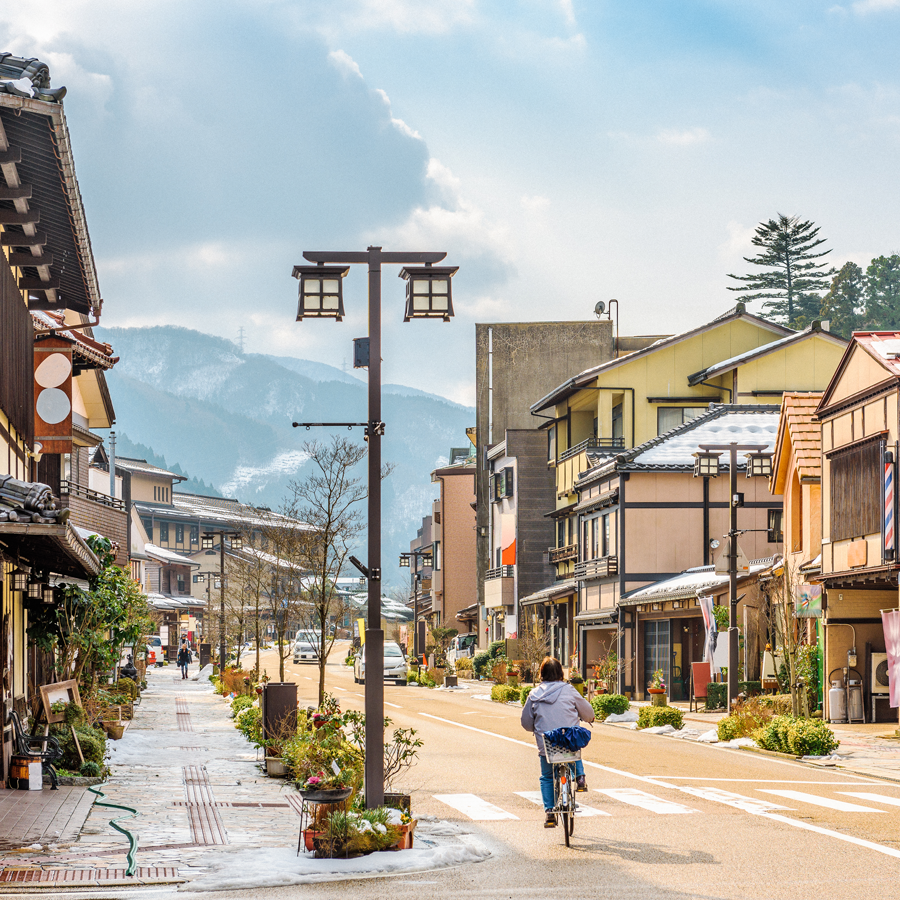
YAMANAKA SHIKKI 山中漆器
The small resort of Yamanaka Onsen has not only been immortalized in numerous haiku by the famous Japanese poet Bashō extolling the virtues of its rejuvenating waters, but is also known for its rich lacquer art heritage. Nestled in the mountains of Ishikawa Prefecture on the northwest coast of Japan, the humid climate of Yamanaka Onsen is particularly well suited for working with natural Urushi lacquer. The origins of Yamanaka shikki, or lacquerware, can be traced back to about 1580, when a group of woodworkers from the nearby town of Echizen came here, specializing in the art of rokuro-biki (轆轤挽き) - turning wood on a lathe. The goods they made were sold as souvenirs to tourists to the onsen hot springs, and the area soon became known for its fine lacquerware, especially tea ceremony accessories.
Urushi 漆
Production
1. Kidori
Cutting the wood into round slices, all the wood used by Gato Mikio comes from Japan.
2. Arahiki
Cutting out the rough shape, then drying for 50-60 days, reducing the water content of the wood by about 12%. This mainly prevents the wood from deforming after finishing
3. Nakaarahiki
More accurate cutting of the mold (3mm larger), another 30-60 days drying to reduce again about 10% of the water.
4.Shiage hiki
Precise, final cutting and decorating of the parts by hand
5. Kijigatame
Applying a first coat of varnish, which soaks into the wood and also prevents deformation.
6. Nugui urushi(wipe off Urushi)
Application of the final layers of varnish and polish. Depending on the product, this final step is repeated a different number of times until the desired thickness and color of the lacquer is achieved.
Care and cleaning
Lacquerware should only be cleaned with a soft sponge or cloth and mild detergent. After cleaning, the product should be dried thoroughly with a cloth. Excessive drying can damage the lacquer, ideally lacquerware products are used often and cleaned damp to keep the lacquer and wood like new for a long time.